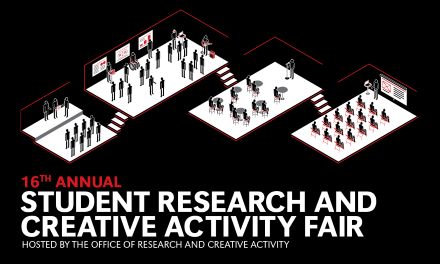
Advisor Information
Jorge Zuniga
Location
Criss Library
Presentation Type
Poster
Start Date
1-3-2019 10:45 AM
End Date
1-3-2019 12:00 PM
Abstract
For many surface EMG (sEMG) prosthetic control systems, the muscles on the affected limb are used to trigger the control system. This can lead to fatigue in the user as they have to maintain continuous muscle activation and coactivation in order to achieve prosthetic control [3]. The crux of any prosthetic control system is the human machine interface that is developed, and at present many control systems have complicated interfaces that limit the degrees of freedom of the prosthetics. This study focuses on the development of a low-cost prosthetic control peripheral that is compatible with the prosthetics developed by Dr. Zuniga and his research team.
To simplify this interface, a simple, low-cost, low-profile, wearable platform was developed with an off-the-shelf MyoWare Muscle Sensor to allow for custom commands to be sent to a prosthetic control board. The printed circuit board (PCB) was designed using EAGLE EDA and incorporates a battery, with charging circuit, dedicated power supply, microcontroller, and a MyoWare. This is shown in figures one and two.
The power consumption of the device was measured and the battery life was calculated for six different battery sizes over a twelve hour period. A standard battery life equation was used for this.
Creative Commons License
This work is licensed under a Creative Commons Attribution 4.0 License.
Files over 3MB may be slow to open. For best results, right-click and select "save as..."
Included in
Biomedical Commons, Electrical and Electronics Commons, VLSI and Circuits, Embedded and Hardware Systems Commons
An Electrooculography Prosthetic Control System
Criss Library
For many surface EMG (sEMG) prosthetic control systems, the muscles on the affected limb are used to trigger the control system. This can lead to fatigue in the user as they have to maintain continuous muscle activation and coactivation in order to achieve prosthetic control [3]. The crux of any prosthetic control system is the human machine interface that is developed, and at present many control systems have complicated interfaces that limit the degrees of freedom of the prosthetics. This study focuses on the development of a low-cost prosthetic control peripheral that is compatible with the prosthetics developed by Dr. Zuniga and his research team.
To simplify this interface, a simple, low-cost, low-profile, wearable platform was developed with an off-the-shelf MyoWare Muscle Sensor to allow for custom commands to be sent to a prosthetic control board. The printed circuit board (PCB) was designed using EAGLE EDA and incorporates a battery, with charging circuit, dedicated power supply, microcontroller, and a MyoWare. This is shown in figures one and two.
The power consumption of the device was measured and the battery life was calculated for six different battery sizes over a twelve hour period. A standard battery life equation was used for this.